DYEING
Our state-of-the-art Dyeing department, equipped with cutting-edge technology, boasts a remarkable production capacity of approximately 15,000 Kgs of dyeing per day. This enables us to seamlessly fulfill all our dyeing requirements. Our array of dyeing machines caters to various fabrics, including cotton, while our fully computerized high-temperature jet-dyeing machine is adept at handling synthetic fabrics such as polyester and nylons.
Ensuring precision in every aspect, our well-equipped Processing laboratory conducts thorough Lab tests to meet stringent parameters. The dip dyeing process is tailored to specific requirements, guaranteeing Ready-for-Testing (RFT) results with an ultra-low liquor ratio, contributing to energy and environmental conservation. The Dye House offers an extensive range of washes and finishes.
Within the Fabric Processing Division, which boasts a daily dyeing capacity of 15,000 kgs, we employ top-notch equipment, including Sclavos, Fong’s, and THEN Airflow dyeing machines. This division is adept at dyeing both 100% cotton and blended fabric. The flexibility in machine size selection allows us to handle lot sizes ranging from 10 kgs to 500 kgs. Additionally, the department features two finishing lines from Brueckner Germany and one from Santex Switzerland, complemented by hydro extractors, Fongs BSD dryers, and Ferraro Italian compactors.
Maintaining the highest standards in fabric quality, Our Dye House incorporates a Quality Control laboratory equipped with the latest tools to assess fabric performance. Our commitment to excellence ensures that every processed fabric meets and exceeds industry standards.
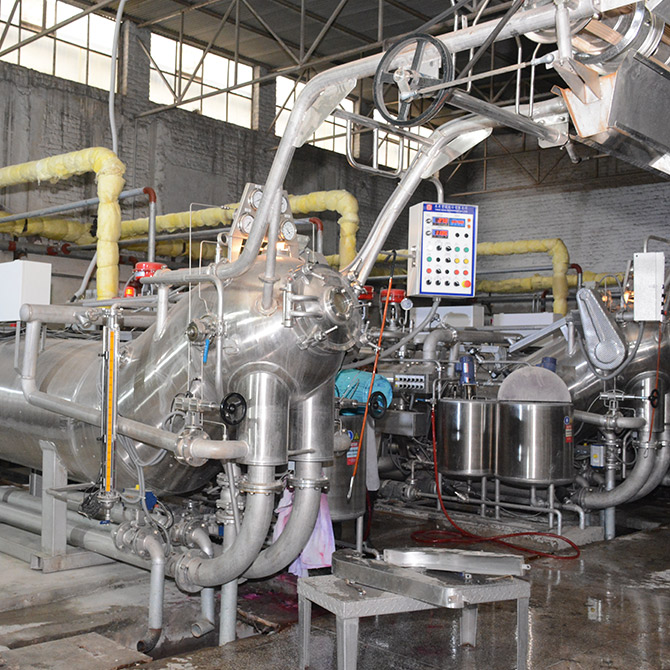
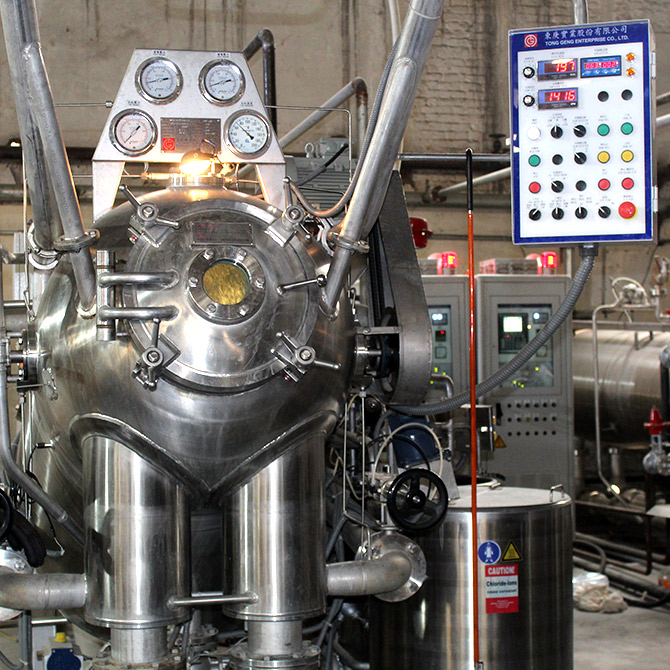
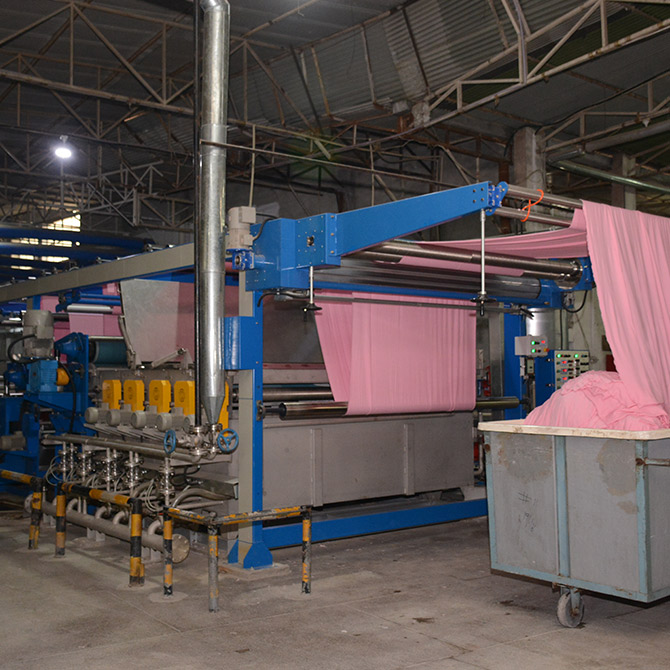
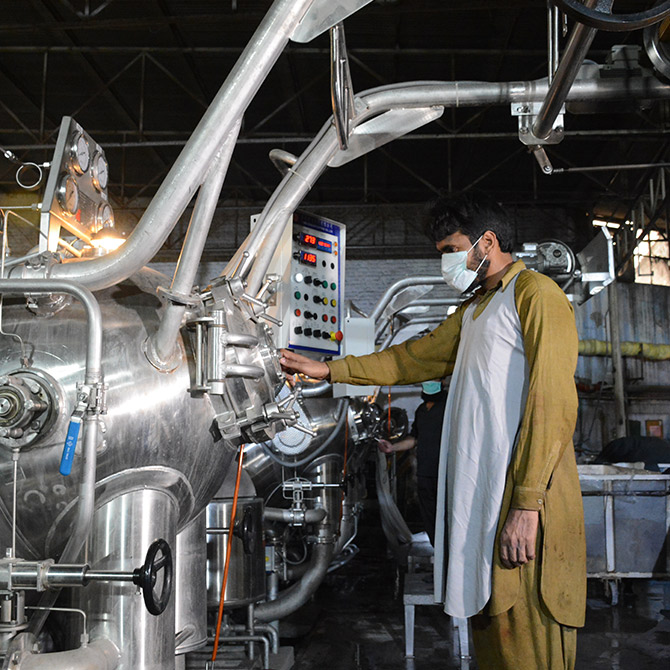
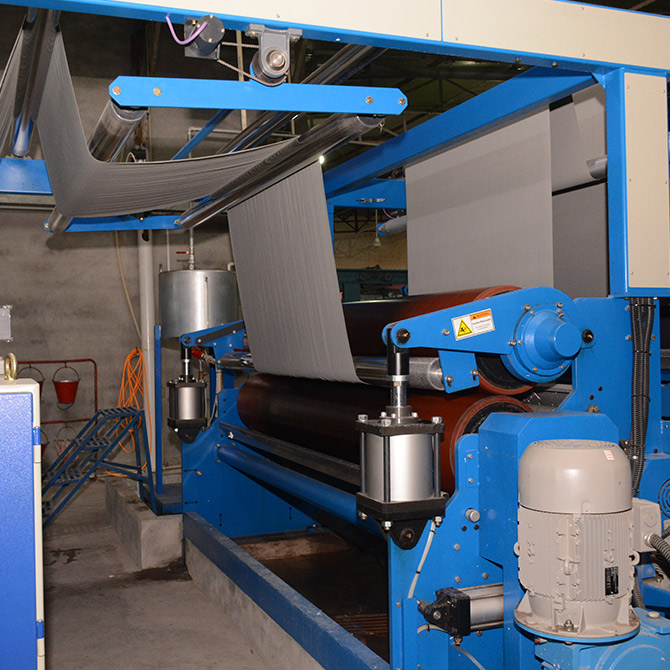
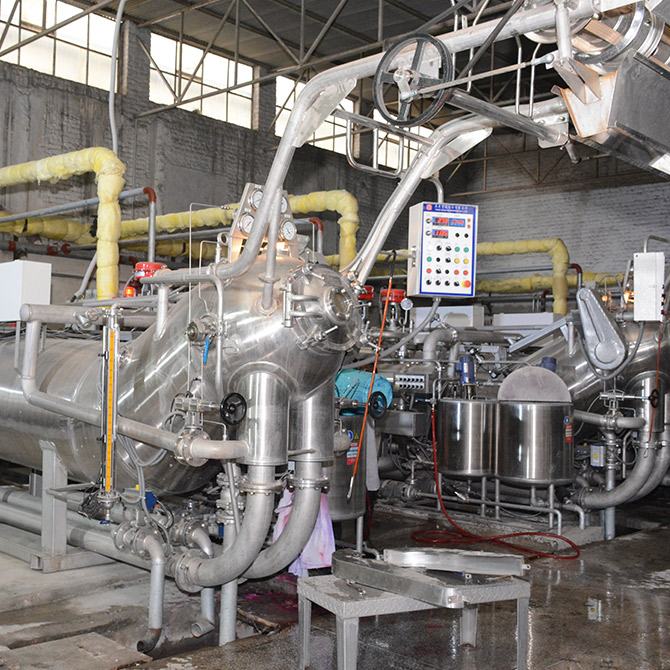
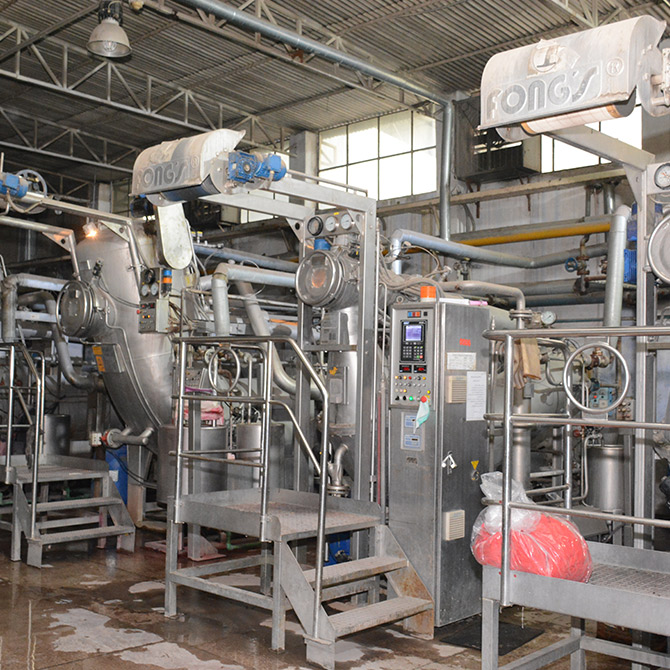
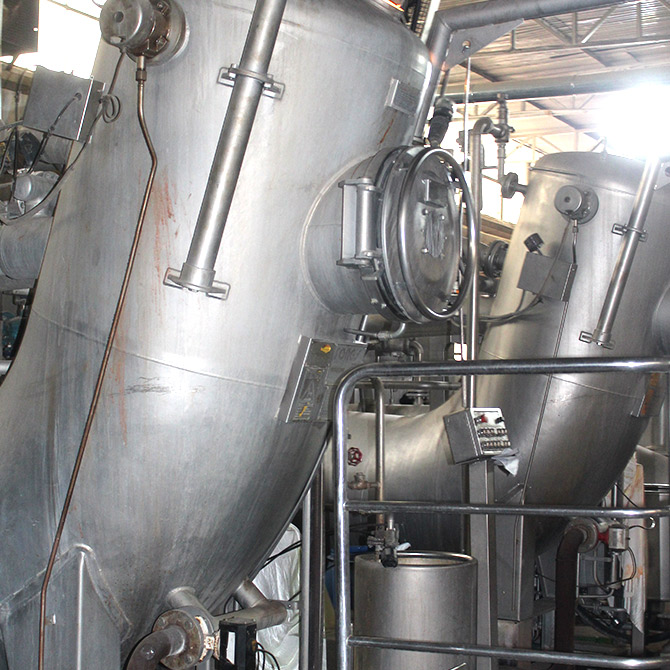
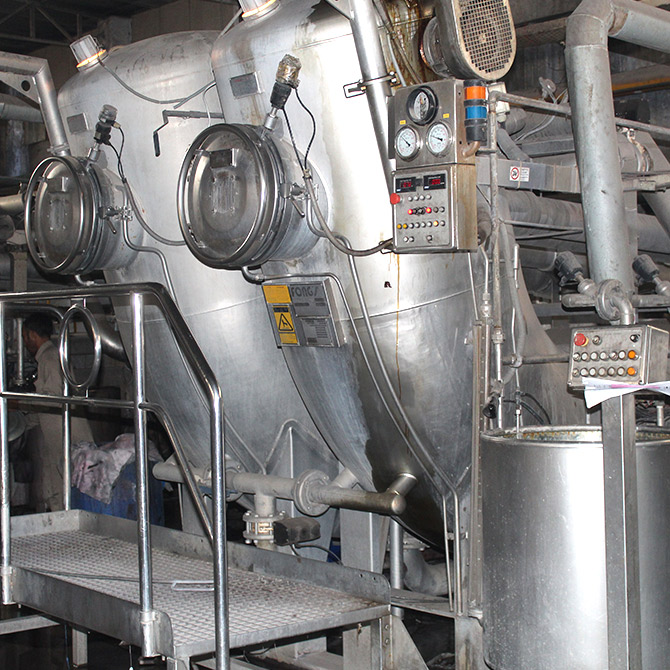
FINISHING
Our Finishing department is equipped with cutting-edge technology to ensure the highest quality outcomes. Automatic hydro-extractors cum slitters from Corino Italy efficiently remove moisture from dyed fabric. For instant fabric drying, we employ computerized tensionless Santex and Fongs BSD dryers. To exercise precise control over shrinkage, our department features fully computerized Italian Ferraro compaction machines. Tumble dryers are utilized to achieve minimum shrinkage values.
Our commitment to excellence extends to the personal attention given to each fabric leaving the finishing department. Rigorous inspection and thorough checks for relevant factors are conducted to guarantee that the fabric meets our stringent quality standards before progressing to the next stage of production. This meticulous approach ensures that only the highest-quality finished products move forward in our production process.
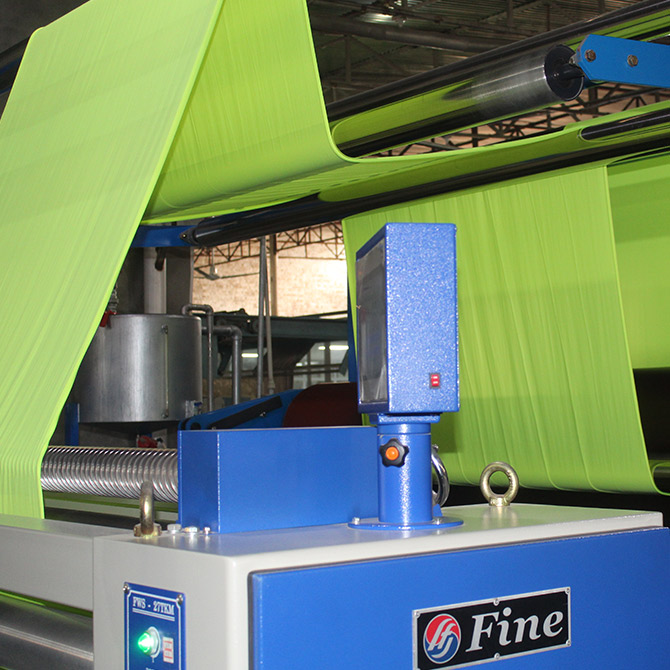
QUALITY CONTROL LAB.
Our dedicated team of highly qualified and experienced technicians employs the latest equipment to uphold stringent international performance, safety, and environmental standards in the manufacturing of apparel for renowned brands such as Adidas, Under Armour, Fruit of the Looms, Rawlings, Alleson Athletic, and Augusta Sports. This commitment ensures that the fabric quality aligns seamlessly with the specified parameters of our customers.
Garnish Sports has meticulously documented a comprehensive Quality Manual that articulates the organization’s quality management system. The management team establishes a detailed quality plan, delineating specific quality practices, required resources, and the sequence of activities pertinent to each product. Rigorous quality checks are implemented at every stage of the manufacturing process, spanning Yarn, Fabric, Processing, Cutting, Stitching, and Packing.
Prior to cutting, a thorough examination is conducted to ensure compliance with customer standards, encompassing factors such as shrinkage, GSM, shade, and more. Our in-house laboratory is fully equipped and computerized, boasting the capability to conduct a wide array of tests. These include Colorfastness to Wash, Colorfastness to Water, Colorfastness to Rubbing, Colorfastness to Perspiration, Dimensional Stability, Spirality, Fabric Weight, pH value, Bursting Strength, Garment Durability, and Print Durability tests, among others. This exhaustive testing regimen underscores our commitment to delivering products that not only meet but exceed the expectations of our valued customers.

PROCESSING LAB
The Garnish Sports Processing Lab boasts state-of-the-art technology, including the world’s latest Automated Lab Dispenser, “Robolab,” with an impressive error margin of only 0.0001%. Our lab is further enhanced by the incorporation of the latest Datacolor water and Air-cooled IR Lab Dyeing machines, ensuring precision and efficiency in our processes.
To achieve meticulous color matching, we utilize the latest Spectrophotometer by Datacolor, complemented by assisting software seamlessly linked with production, known as “SDM” by Sclavos. This integration of cutting-edge equipment and software not only enhances our color-matching capabilities but also streamlines the overall production process, aligning with our commitment to delivering high-quality results to our clients.
At Garnish Sports, we prioritize staying at the forefront of technological advancements in our field, ensuring that our processing lab remains a hub of innovation and accuracy for all our dyeing and color-matching requirements.
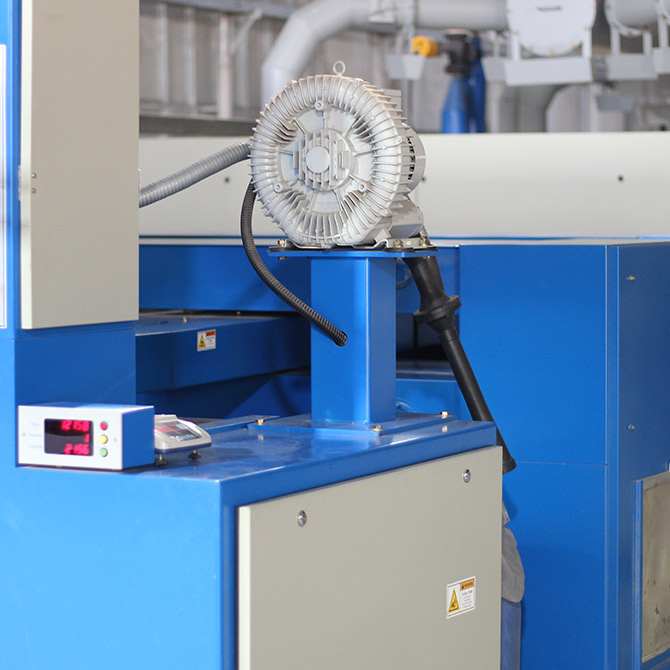